While experiencing significant growth, we needed to migrate our Los Angeles facility into a 14,000 square foot data center space, but we were up against some barriers: shallow raised floors and low ceilings. Also, it has always been important to minimize our footprint and wanted to continue that trend. Within our facility, the uncontained hot/cold aisles were limiting our ability to support increasing demand for higher rack densities. The convenient, but inefficient solution, of adding more air conditioning was not an option because we were growing and needed to support additional clients. It was a struggle to maintain equipment operation with that setup. Our CEO, Sam Scott, “wasn’t OK with just buying more cooling”.
The Challenge
Sam was determined to create a new data center solution that would support higher rack densities within acceptable operational temperatures. The problem was approached from two perspectives. The first challenge was increased rack density. At current 200 watts per square foot, we needed to reduce the physical white space of the data center in order to achieve higher rack densities. The white space was then constrained to 10,000 square feet to enable double the rack density at 4 – 5 kW per cabinet (20 square feet per rack). Increasing demand for higher rack densities drove us to deploy a reliable data center infrastructure comprised of cabinets and cabinet-level containment. The second challenge was cooling. At those higher rack densities, adding more air conditioning to the room was not an effective option. We needed to find a solution that would provide ideal airflow to cool each rack despite the fact that the room had low drop ceiling and shallow raised floors, which limited the amount of airflow volume into the room.
The Solution
The team at Chatsworth Products International presented their Passive Cooling technology, a technique that completely segregates hot and cold air, and can be applied at the cabinet or aisle level, providing increased equipment cooling performance in all elements of our data center mechanical plant. It also reduced our overall energy costs. CPI’s F-Series TeraFrame® Cabinets with Vertical Exhaust Ducts were the selected solution. The F-Series TeraFrame Cabinets are highly configurable and functional racks, providing a 3,000 lb. (1360 kg) load rating. Ducts within the cabinets channel hot exhaust air out and up into the drop ceiling, separating the hot air out of the room, and ducting it back into the Computer Room Air Conditioner (CRAC) units. The cooled air from the CRAC units is redistributed under the floor, into the room and through the racks. This cools the equipment without the need to overprovision the room. For us, this setup was a dream come true. We couldn’t operate at the level we do without these cabinets.
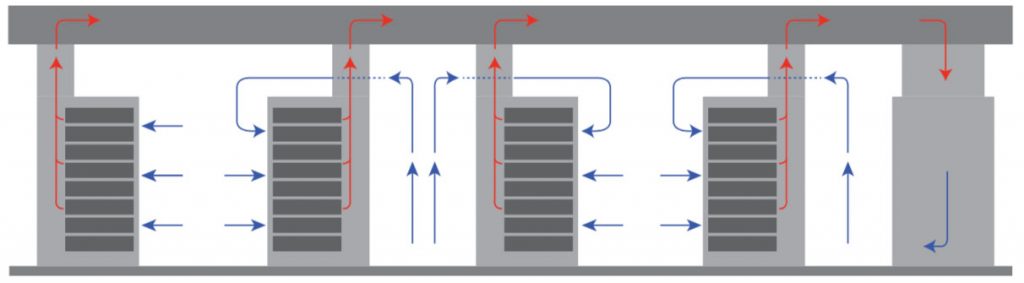
We were thrilled because we saw the improvement immediately once we implemented the cabinets. It allowed us to fully service our clients. Clients pay per footprint of the cabinet space, and when the limitation is compute power and ability to cool that power—if you can’t support that—they’ll look elsewhere. Our clients are always at the forefront of our minds when making these types of business decisions. It’s important to us to consider how we can continue to provide them with the best services and support them in their business needs.
To learn more, read the complete case study or listen to the webinar with Sam Scott and John Thompson with CPI.